Apprentices helped Lewis Hamilton win his fifth Formula One championship
- Emma Finamore
- 04 Nov 2018
They work in the Mercedes factory as part of nine operational departments, keeping Hamilton on the road.
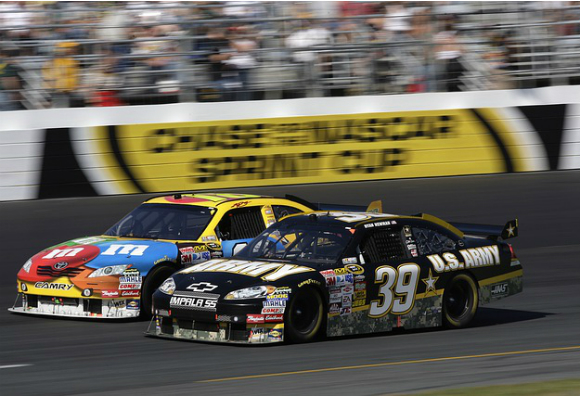
Lewis Hamilton won his fifth Formula One championship with a fourth-place finish at the Mexican Grand Prix in October, and apprentices were a key part of his success.
Apprentice trainees work in the Mercedes factory, as part of nine operational departments, keeping Hamilton and Mercedes the dominant force of the current car racing era.
Arch Apprentices, together with Mercedes-AMG Petronas Motorsport, has created an infographic to break down the sub-departments in which apprentices work during a two-year scheme in the Operations sector and how the output of these departments impact the team and drivers – helping them to win races and championships. They are the crew behind the drivers.
The AMG Apprenticeship
The Mercedes scheme starts advertising in March and begins in September of that year with around seven apprentices joining one of the operational departments based at the team’s headquarters in Brackley, Northamptonshire.
The departments within the operations area are the Car Build, Electronics, Machine Shop, Composites, Pattern Shop, Paint Shop, Model Shop, Rapid Prototyping, and Non-Destructive Test & Development.
The five-time Formula 1 champions’ scheme sees candidates work towards a level-three qualification in crucial areas of the team’s performance, that ultimately help drivers Lewis Hamilton and Valtteri Bottas win races and perform to their maximum.
The Machine Shop focuses on metallic parts within the car and can oversee anything from wheel nuts to gearbox casings and will create tens of thousands of parts per year.
Formula 1 Focus
The focus and impact of the work apprentices in the scheme will handle is wide-ranging, having an influence on branding, build, safety or performance.
The areas in which apprentices work with Mercedes are split across five sections. The first is the Car Build department, which strips the car of all components following a race to check and inspect them before reassembling the cars ahead of the next event.
Composites, which also includes the Pattern Shop, produce all carbon fibre parts that feature on the cars, which include the monocoque that protects the drivers. The Pattern Shop creates patterns from which are made moulds that produce the vital carbon structures.
The Machine Shop focuses on metallic parts within the car and can oversee anything from wheel nuts to gearbox casings and will create tens of thousands of parts per year. In tandem with this department, as well as Composites, is the Testing Department which identifies any damaged components or those containing damage issues.
The Rapid Prototyping and Model Shop work together on wind tunnel models and the parts that will be tested in it on scale models. Together, they trial aerodynamic parts that may end up on the actual race car, in the hope of improving performance.
The Electronics Department handles some of the most critical aspects of the car, the electrical systems such as the steering wheel and brake by wire. With much of the car dependant on these systems, as well as the driver’s race information, this department is vital.
The Paint Shop takes care of painting the cars and all the team’s equipment, garages and hospitality while also overseeing branding, decals and printing.
News
- Lancaster Royal Grammar School Win the EY Arcade
- Parents’ Perceptions of Apprenticeships Changing
- Alesha Dixon & Akala are giving careers advice on YouTube
- A former government adviser says school leavers should get £20,000 to stay in training
- Five Day Warning: UCAS Deadline Fast Approaching
- Young People Face Work Experience Post Code Lottery
- School leaver blog: work shadowing, breweries and more
- A-level results 2015: record number of people taking up university places
- This Head of Year 11 sat the new, harder maths GCSE & only got a C grade
- Online university offers free degrees to Syrian refugees